刃物選び
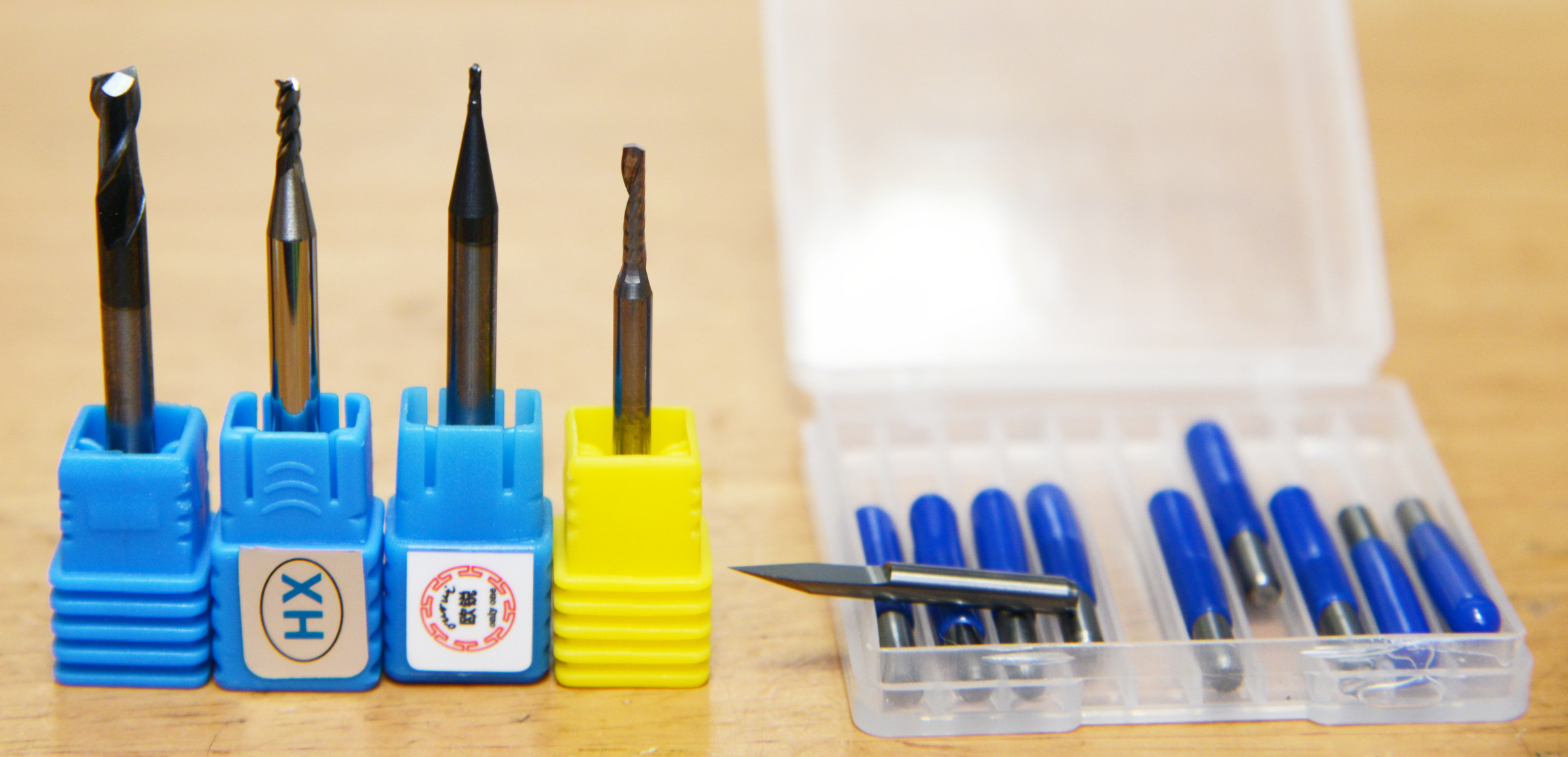
CNCでは、対象を削るための刃物(エンドミル)が必要になる。これがなかなかに悩ましい。細いエンドミルでなければ細かい形状が作れないし、しかしそれだとたくさん削るときに時間がかかりすぎる。また、後述するように深穴を掘るのも難しい。結局、複数のエンドミルが必要になるし、また1つの対象を加工する途中で交換する必要もある。
今回購入したCNCには刃物が3種類、12本付属していた。1つは上の写真の右側に写っている彫刻用のもの(10本同じもの)で、先端がV字型になっているものだ。これは主に彫刻(表面への文字入れ等)に用いるもので、大きく加工するのには向いていない。また他に2本、直径2mmのスクエアエンドミルが付属していた。黄色いホルダーに刺さっているものと、青のホルダーのうち中央のものである。確かに2mmは中間的な太さで、薄板からの切り出しのほか、全体に削って減らすのにも、細部の形状を出すのにもそこそこ使える。しかし、刃先と軸の径が異なっているので、深い穴や厚い板を切ることはできない。そこで、別途2本のエンドミルを購入した。
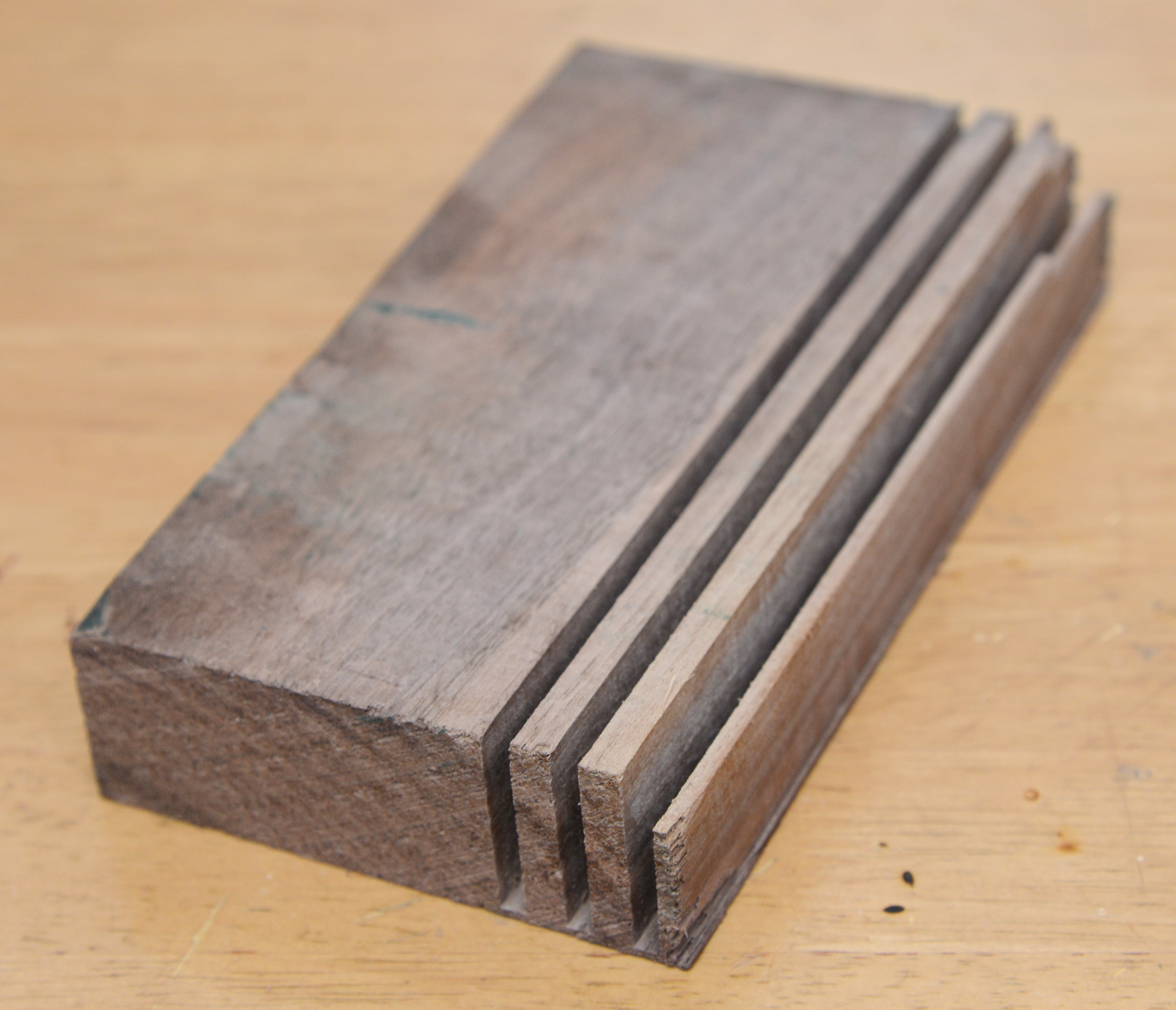
1つは深穴を掘るためのもの(左端)で、軸と刃先の太さがともに4mmなので(チャックに干渉するギリギリまで)深い穴を掘ることができる。全長とコレットの関係から、このエンドミルなら上の写真のように約30mmの深い穴や溝を掘ることができる。また、深いくぼみ(ポケット)を掘るときに、くぼみの壁面を垂直にすることができる。ただしポケットの角は刃先の半径と同じRがついてしまう。
もう1つは仕上げ用に購入したもので(左から3本目)、直径1mmのボールエンドミルである。刃先が丸いので曲面的なものを削り出すのに向いている。ただしどうしても、軸の部分が刃先よりも太くなるので、奥まったところのRを細かくするのは難しい。
刃物を途中交換するなんて面倒だ、と思っていたが、やってみると、所望の形状を得るためにも、また加工時間を短縮するためにも交換が必須だと気づく。理屈の上では、軸も刃先も細いエンドミルを使い、時間さえかければ深いポケットの角も正確に仕上げられそうだが、そういう長くて細いエンドミルは折れやすくなってしまうし、力がかかると曲がるので、加工の精密度も落ちることになる。どうやっても加工できない形状はできるので、結局、設計時に配慮するしかない。形状の自由度が高く、オーバーハングもある程度までなら作れてしまう3Dプリンタとはやはり別物だと言えよう。
軸の太さが異なるとコレット(チャックの内側の部品)を交換しなくてはならないのも要注意だ。コレットは少し交換しづらいので、刃物を交換するなら同じ軸径のほうが楽になる。上の写真のうち、V字の彫刻ビットと黄色いホルダーが 1/8 インチ、つまり 3.175mm で、青いホルダーが軸径4mmのエンドミルだ。この手のCNCのコレットチャック(ER11)では、コレットを買えばもっと太い刃物も使えるがモーターに負荷がかかるし、もしモーターが強力でもワークが動いてしまうこともあるので、上の写真のように深穴加工には4mmのスクエアエンドミルがあればまず困らないように思った。
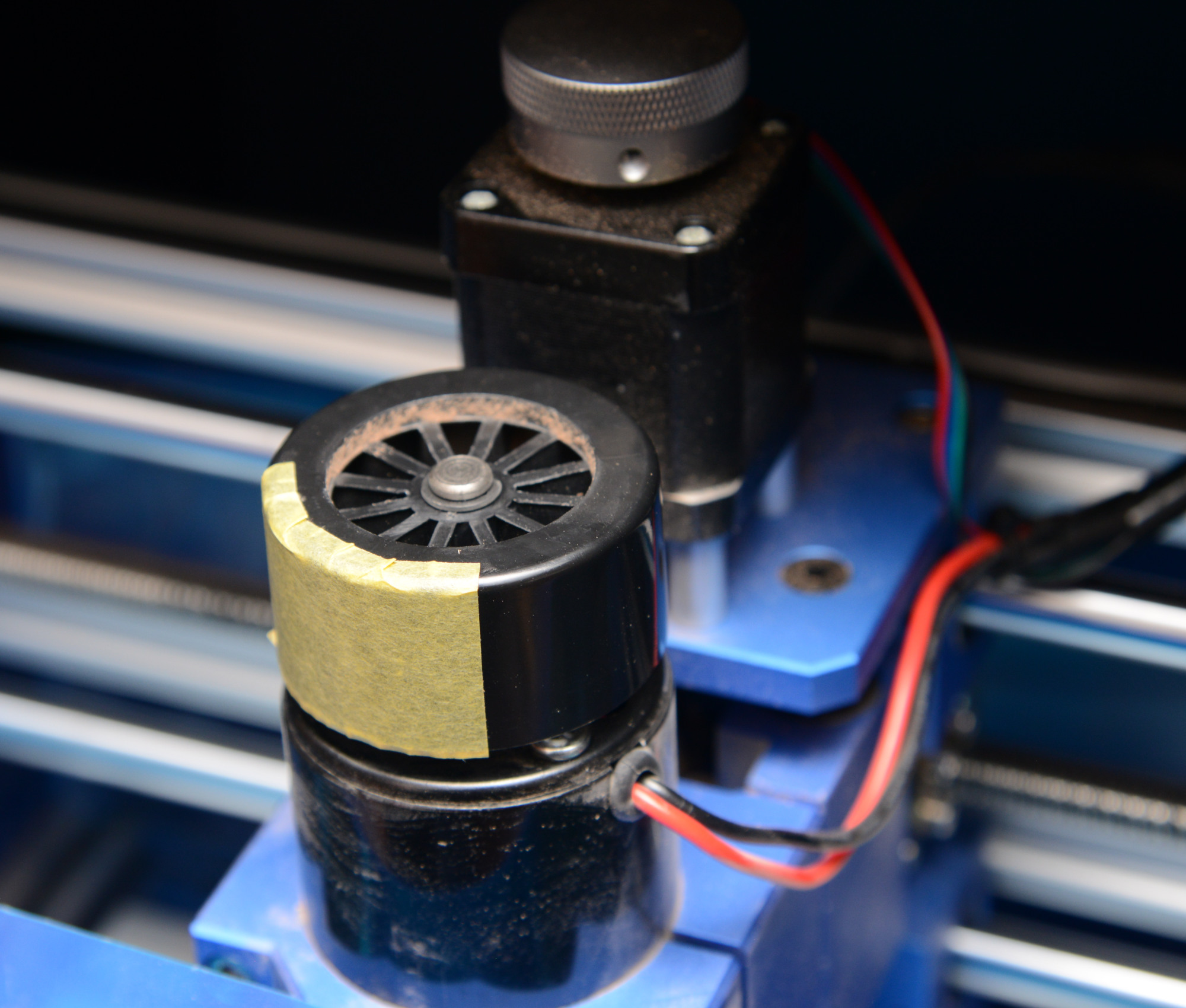
刃先にブレがあると加工精度が落ちるのと、加工時の騒音が大きくなる。そもそも空回しでもかなりの騒音がするが、これはどうやらモーターやコレットのせいではなく、モーターの上に乗っているファンのバランスが悪いためのようだった。そこでモーターを(オフラインコントローラーで)回転させたり止めたりしながら、マスキングテープ片をファンに貼ってバランス取りをしてみた。音や振動が小さくなるように位置を試行錯誤しながら探すだけである。結果、僅かな量(3cm x 4cm ぐらいのマスキングテープ1枚だけ)で大幅な改善を見た。高速回転するので、バランスは重要である。空回しでも振動音が大きかったり、モーターやZ軸あたりを触ってみて振動しているようならバランス取りを試してみるといいと思う。