回路基板(PCB)の作成
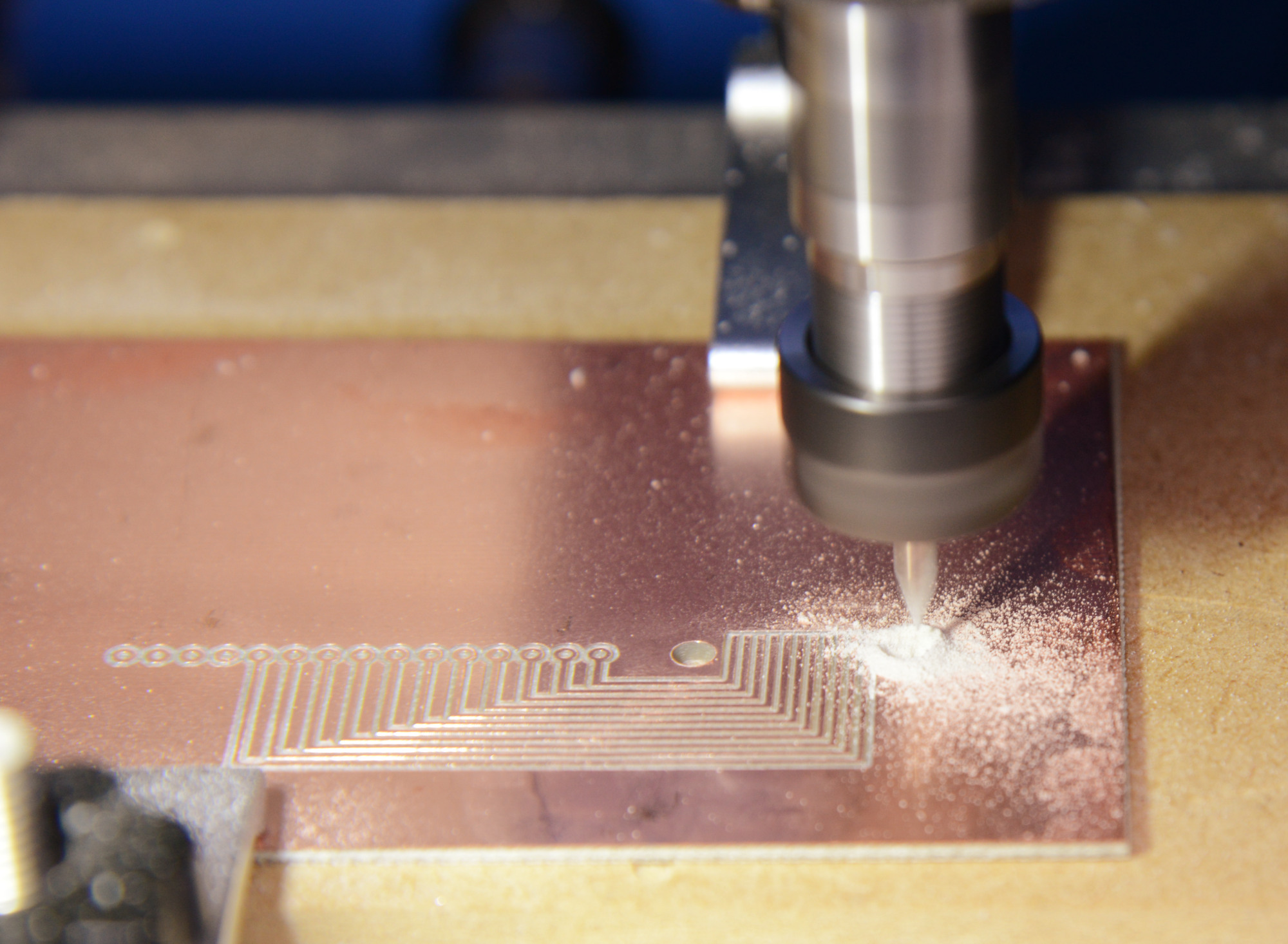
卓上CNCルータの代表的な用途の1つがPCB(電子回路基板, print circuit board)の作成だろう。感光基板を使うなど他の方法もあるし、今は個人の少量の注文も受け付けてくれる作成業者も多く、CNCはそれに比べていろいろな制約があるが、手元でさっと作れるという点には魅力がある。今回、市販テンキーを利用した電卓を作成するためにPCBを作成する必要が生じたので作成にトライしてみた。
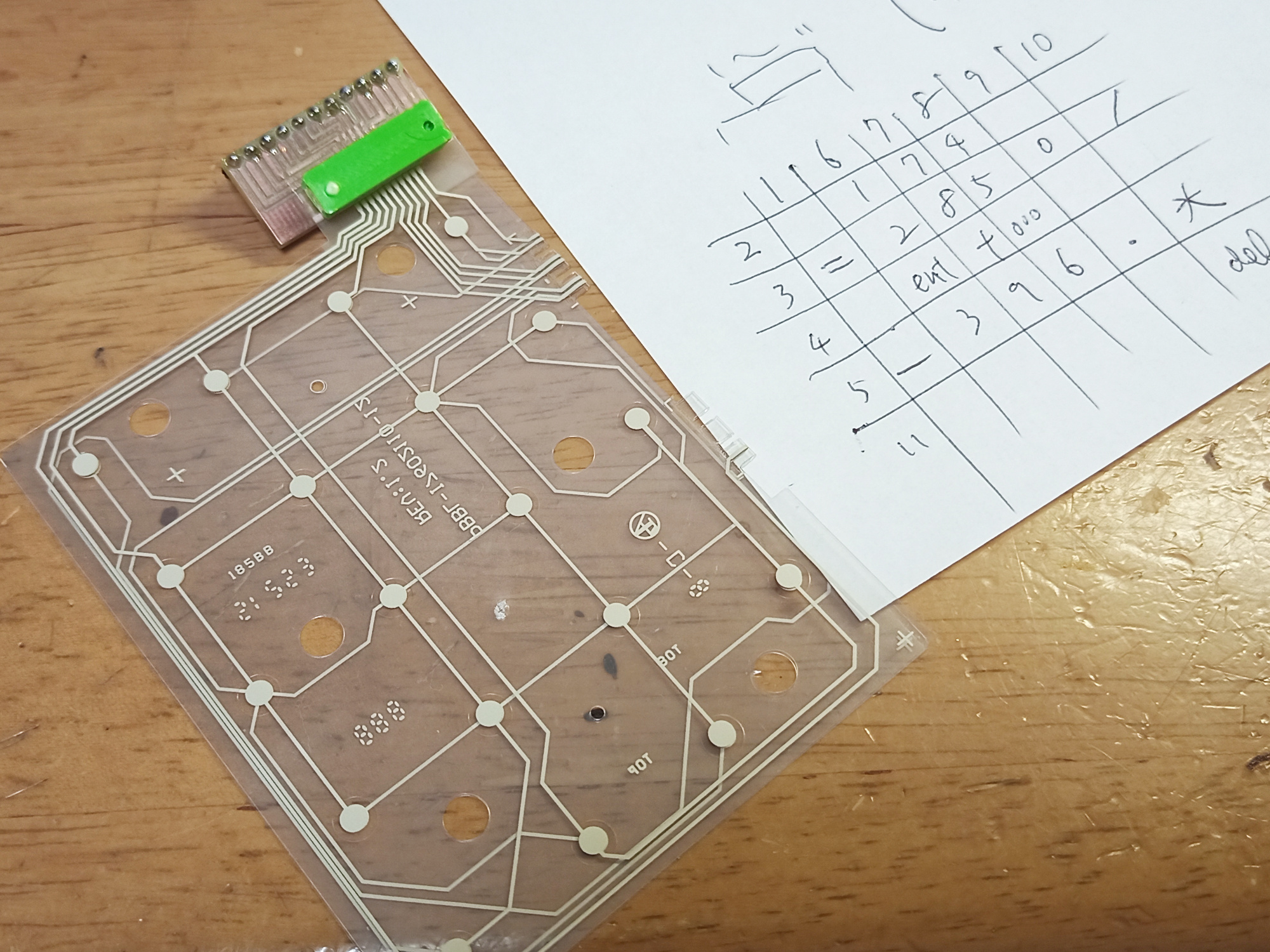
購入した安価なテンキーを分解すると、スイッチ部分はフィルム状になっており、導電部分がプリント基板に圧接される仕組みになっていた。この圧接部分のピッチが1mmだったので、それを接触させ、引き出してマイコンの端子の2.54mmピッチに変換するだけの基板を作成した。回路デザインには専用のCAD(KiCADなど)を使うのが良いだろうが、今回は単純な回路をさっと作るだけなので使い慣れた Blender で立体物として造形し、その輪郭を削るツールパスを Fusion 360 で生成して切削した。最初は上のような小さな基板でちゃんと導通するかを確認し、OKだったので、再度、直接マイコン(Arduino nano)を接続して筐体に格納できるような形状の基板を切削し直した。刃物には彫刻用のVカッターを用いた。切削の深さは浅くても銅箔を切るには十分だが、基板が波打っていると切削深さにむらが出る。導通式のプローブを使ってハイとマップを作成し、補正すると良いようだが、現状ではCNCはオフラインコントローラーで動かしているためそれができない。よって安全を見て0.1mmずつ3回ほど切削して深い切込みを入れたところ、良好な基板が作成できた。
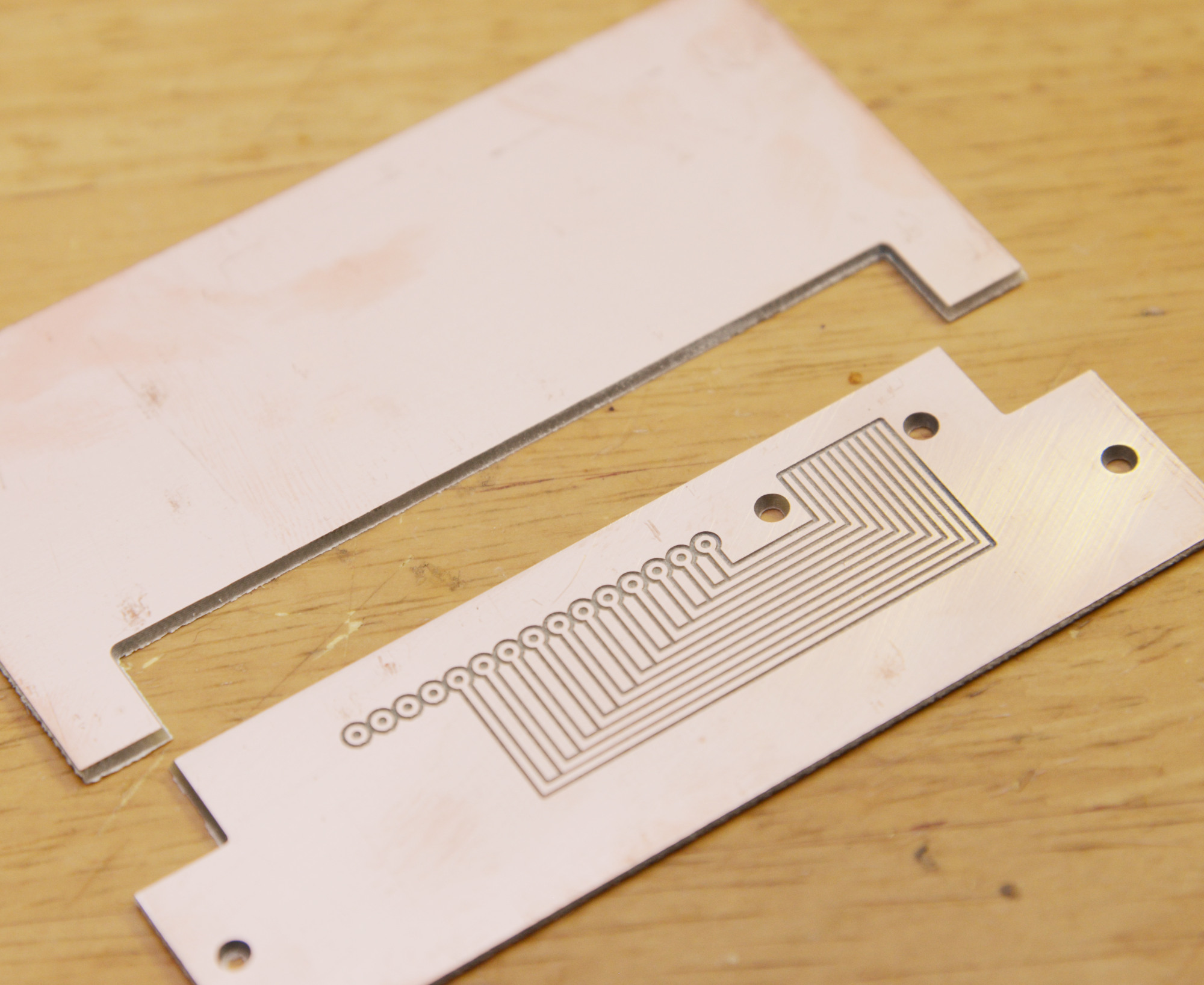
圧接部分にシリコンゴムを押し付ける部品(3Dプリンタで作成した)や筐体に基板を固定するネジ穴と、基板そのものの切り出しは別途、より深く切り込むことで同じ刃物で実現。Vカッターなので切断面が斜めになってしまうが、今回の場合は特に問題になるレベルではなかった。ICのピンを挿す穴は後から手作業で、1mmのドリルで穴あけを行った。カットが深めのため穴にドリルの先がうまくはまり、高精度に穴あけすることができるのはエッチング等で作った場合に比べてメリットがあると感じたが、どうせなら細いエンドミルでピンの穴あけまで全部やってしまうのが望ましいだろう。
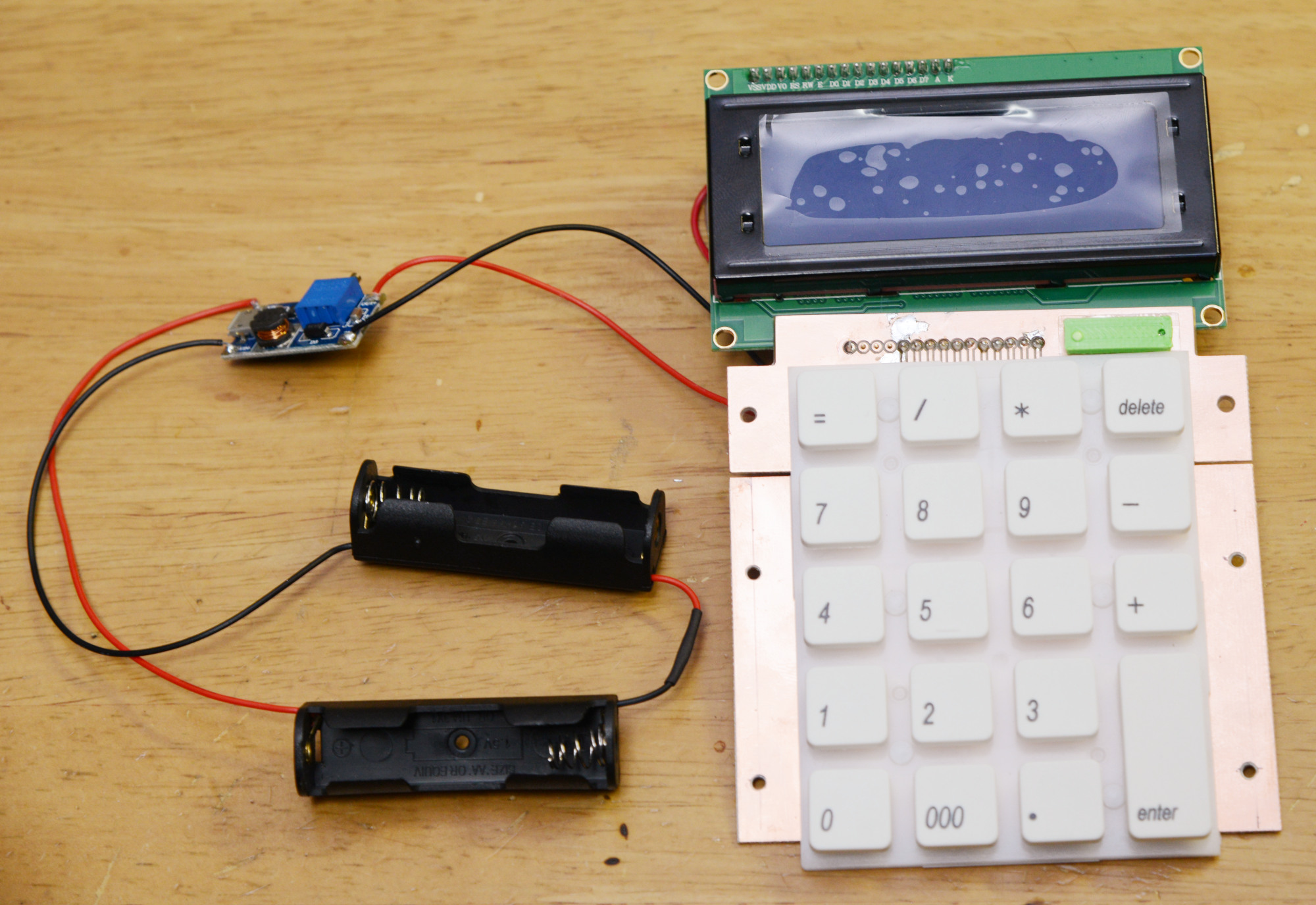
PCBは強度があるので、キーのフィルムを裏から支え、筐体に取り付けるための部品としても使用した。下半分はCNCを使わず手作業で穴あけだけをした基板である。この電卓の制作過程はこちらで紹介している。
今回の基板切削では比較的深く切削したことや、Vカッターの刃先の摩耗、軸のブレなどから、線のピッチが1mm程度(配線0.5mm、あいだの切削部分0.5mm)が安全のように思われた。ICのピンの間を通すにはこれでは不十分である(ピンの穴の直径を1mmとすると、残りの1.5mmをランド、絶縁部分、ランドで分け合うことになる)。また、両面基板を作るには表と裏の位置合わせという問題もあるし、はんだ付けするときに周囲にレジストがないとはんだがつきやすいとか(上の写真でも一部そうなっている)、いろいろ面倒もあり、凝った基板を作るには外注してしまうほうがいいのだろうとは思う。